Sand Casting
Reliable Sand Casting Solutions
At CSG Extrusion, we take pride in offering dependable sand casting services designed to fit the exact needs of various industries—from automotive and construction to marine, electrical, and more. Our sand casting expertise is backed by decades of practical experience, state-of-the-art equipment, and a skilled team that knows their craft inside out. Whether it involves single custom pieces or full-scale production runs, we deliver durable, cost-efficient results. Because we always focus on doing things right, many of our clients choose to stay with us.
As a result, they trust us to provide well-made parts that perform without compromise. A foundry worker carefully pours glowing molten metal from a ladle into waiting molds, while the warm light of the liquid metal reflects off nearby equipment. Meanwhile, on a calm beach, sand sculptures like a crown, some skulls, and starfish surround the word “ALL” carefully written in the sand—a creative reminder of the artistry and precision possible with sand casting services.
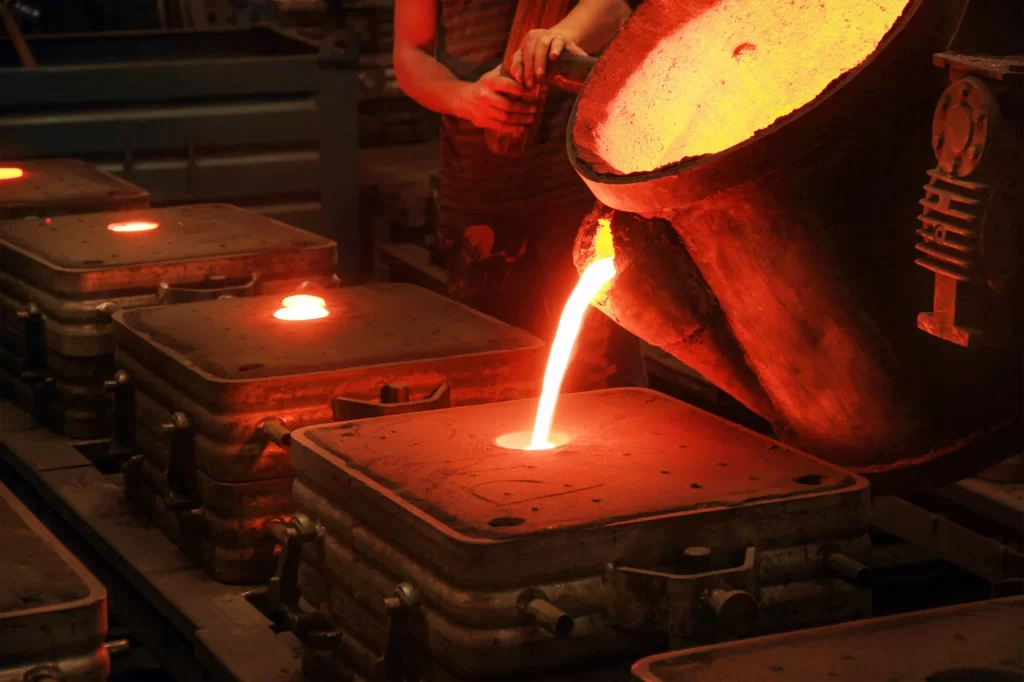
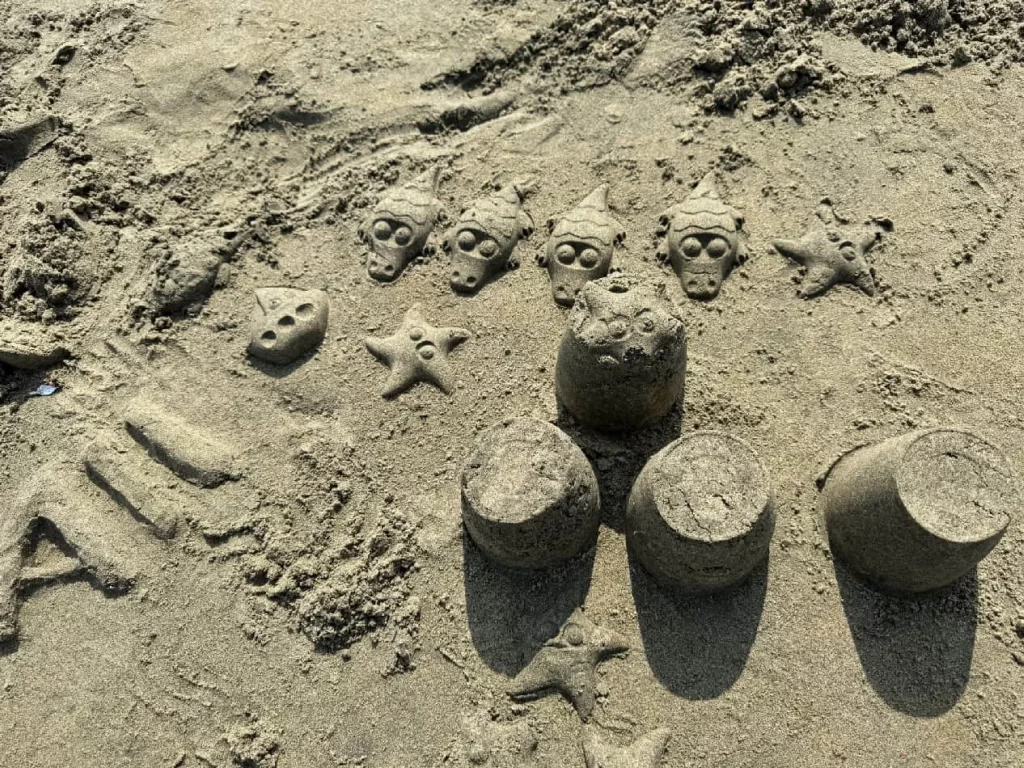
What is Sand Mold Casting?
Sand casting is a very flexible manufacturing method where workers pour melted metal into molds made from sand. This method allows them to create parts with just the right shape and even some custom touches. Moreover, it’s especially handy for making big or complex pieces that need to be both tough and detailed. That’s why many industries stick with sand casting for metals like aluminium, bronze, brass, and good old cast iron, it just works. Also, it suits the production of large or intricate parts that require both strength and fine details, delivering consistent, reliable results across various applications.
Why Choose Sand Casting?
- Versatility: Sand casting works with many types of metals and alloys, making it ideal for producing a wide variety of parts across industries.
- Cost-Effective: It offers an affordable way to manufacture both small and large quantities of parts.
- Design Flexibility: It supports intricate and large-scale part designs.
- Customizable: The mold design adapts to your product specifications.
- Strength: It produces strong parts that handle significant stress and resist wear.
A worker wearing gloves pours hot metal into molds at a factory.
A wooden mold filled with orange clay features a cylindrical metal pipe positioned in the center for casting purposes.
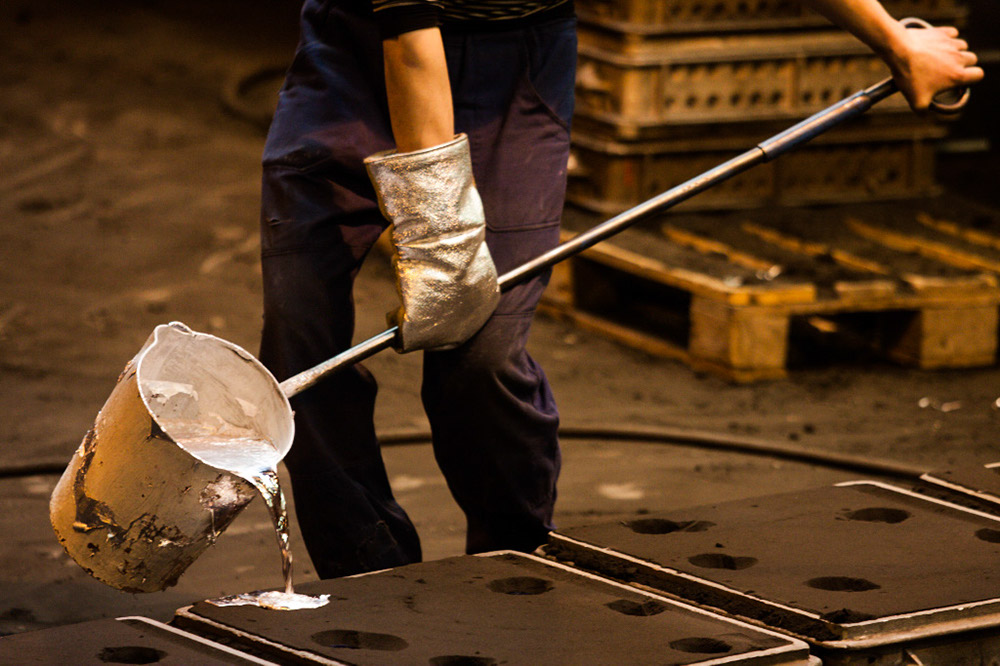
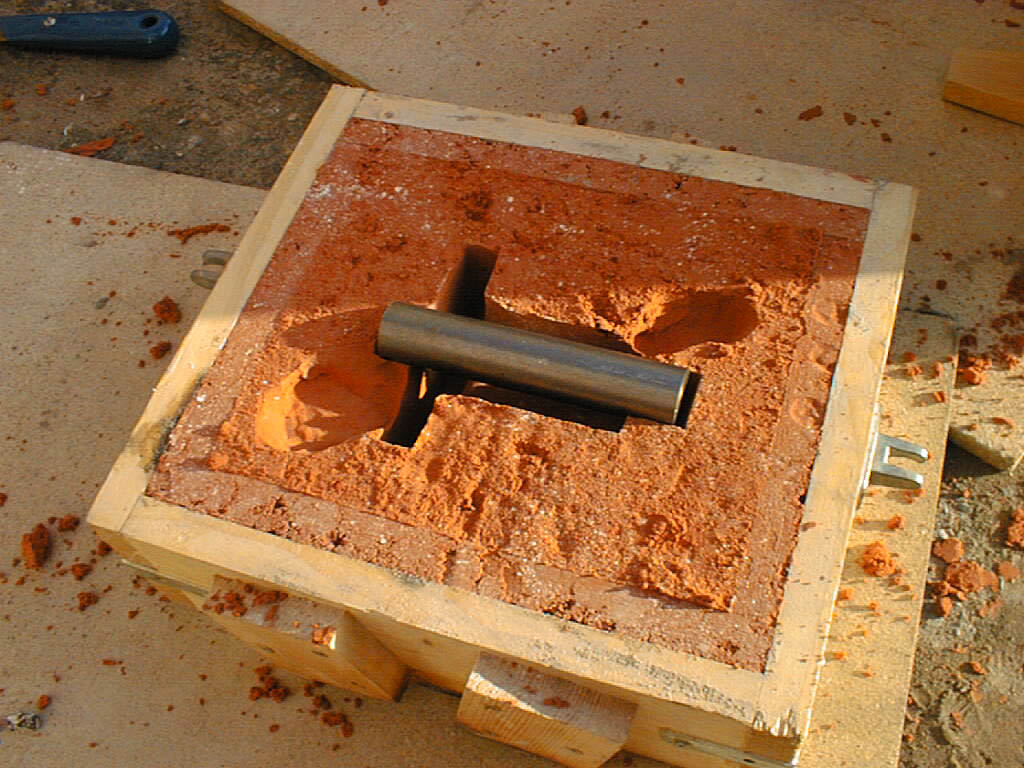
Industries We Serve
- Automotive: Engine components, housings, brackets.
- Construction: Hardware fittings, pipe joints, and structural parts.
- Marine: Impellers, propeller components, and corrosion-resistant parts.
- Electrical: Connector parts, terminal blocks, and insulator bases.
- Heavy-Equipment: Producing base frames, covers, and complex components for various heavy-duty equipment.
Our Sand Mold Process
Consultation & Design – We assess your project needs and design molds accordingly.
- Pattern Making – We create patterns based on your product geometry.
- Mold Preparation – High-quality sand casting molds are formed to precise standards.
- Metal Pouring – Workers carefully pour the heated molten metal into the prepared mold cavity to shape it as desired.
- Cooling & Solidification – The casting cools until it achieves the required strength.
- Finishing – Cleaning, trimming, machining, and final inspections ensure quality.
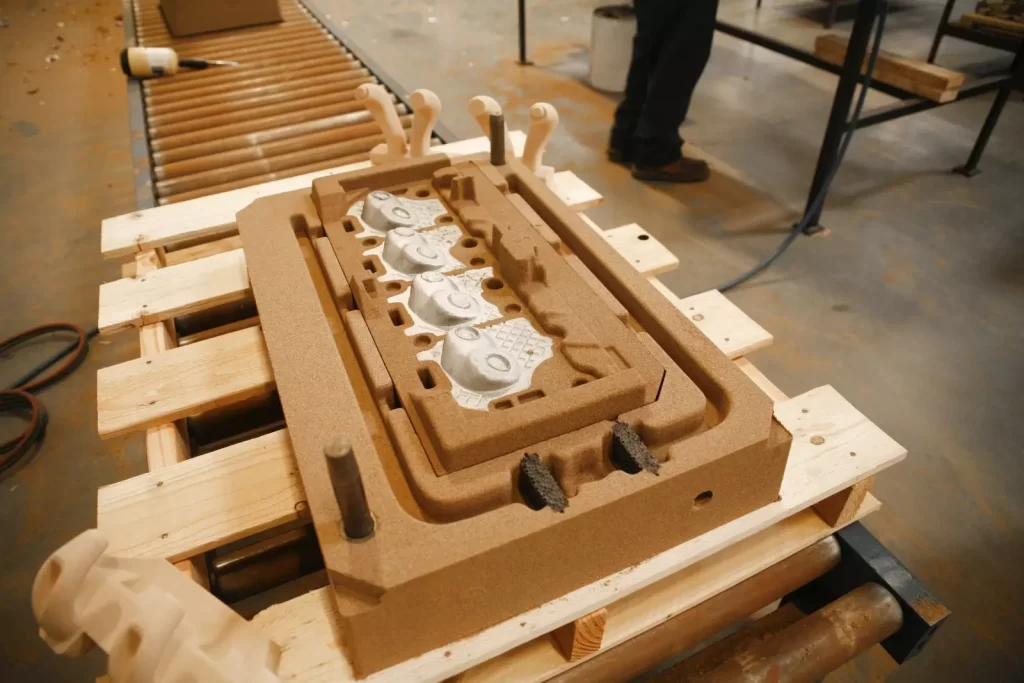