Metal Casting
Metal Casting Services in UAE
Are you struggling to find a manufacturing method that delivers both precision and affordability? Metal casting could be the ideal solution for your business. At CSG Extrusion, we proudly offer some of the Top UAE Metal Casting Services, tailored to meet your unique production requirements. Whether you’re creating complex components or large-scale industrial parts, our advanced metal casting techniques ensure accuracy, strength, and cost efficiency all under one roof.

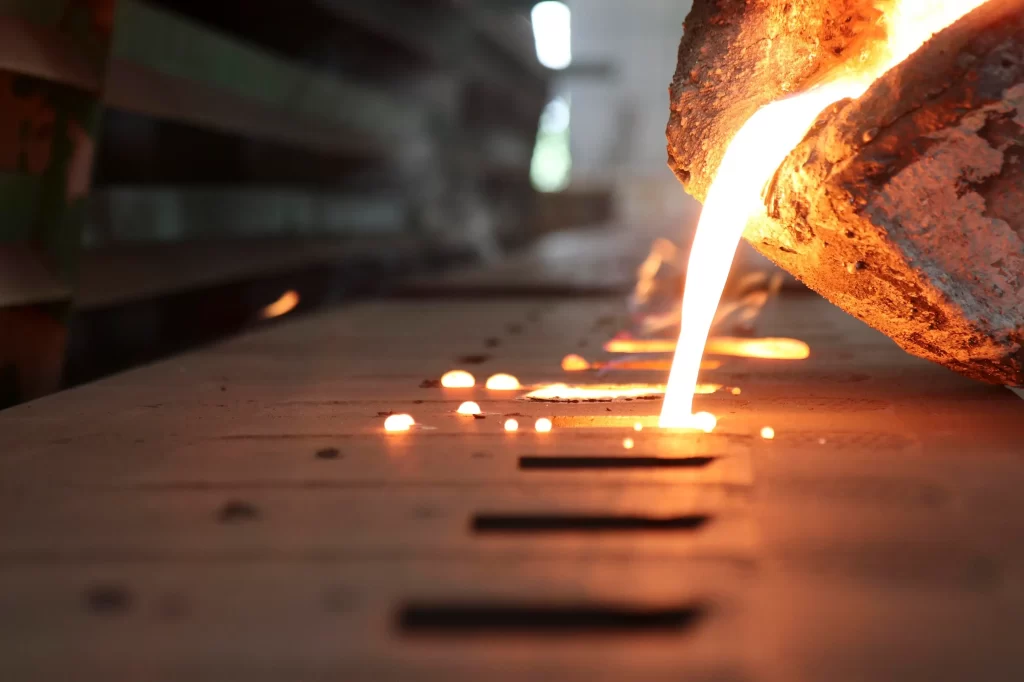
Why Choose Metal Casting?
- Versatility
From finely detailed miniature parts to large-scale structural units, metal casting offers unmatched accuracy and adaptability for projects of any scale or intricacy. - Cost-Efficiency
Ideal for bulk production, casting significantly reduces unit costs once the initial mold is created. - High Strength & Durability
Cast components boast exceptional structural integrity, enduring performance, and an innate resilience to extreme conditions, making them the backbone of reliable, long-lasting applications.
- Complex Shapes
The casting process allows the production of parts with intricate geometries that are difficult or costly to machine.
Metal Casting Process
Mold Design
- Customized mold creation using sand, ceramic, or metal.
- Molten metal flows with precision into the mold, faithfully replicating even the most delicate contours and fine details.
Melting the Metal
- The chosen metal (e.g., aluminum, iron, steel) is heated to a molten state based on the application.
Pouring
- Precise mold design is essential for achieving high-quality end products.
Cooling & Solidification
- Controlled cooling ensures optimal strength and integrity of the cast.
Finishing
- Post-casting processes include trimming, polishing, machining, and inspection to ensure specifications are met.
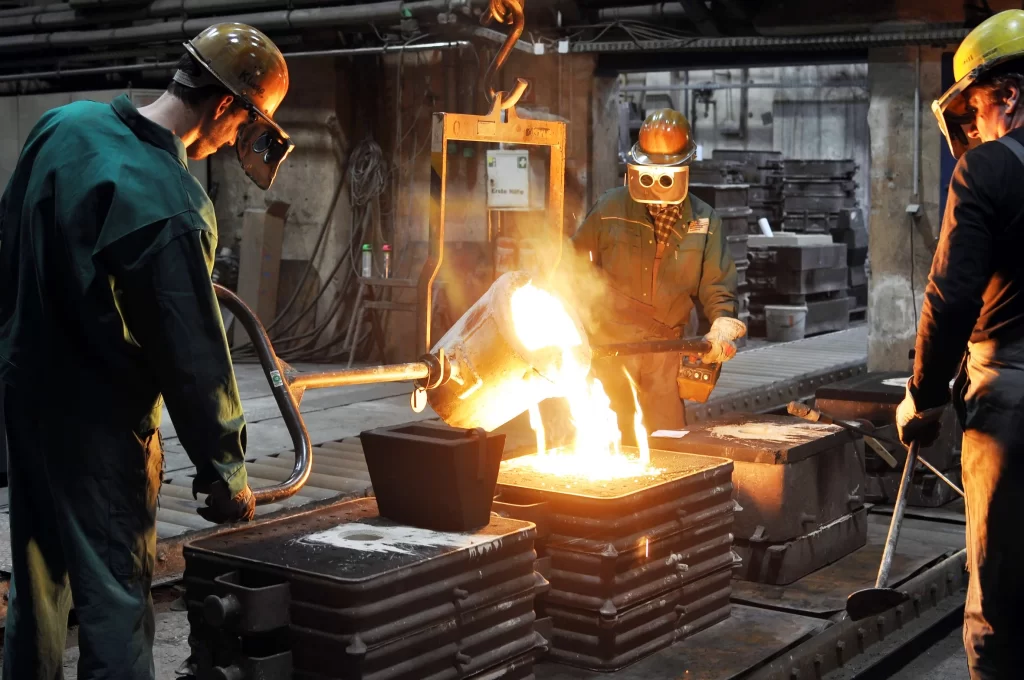
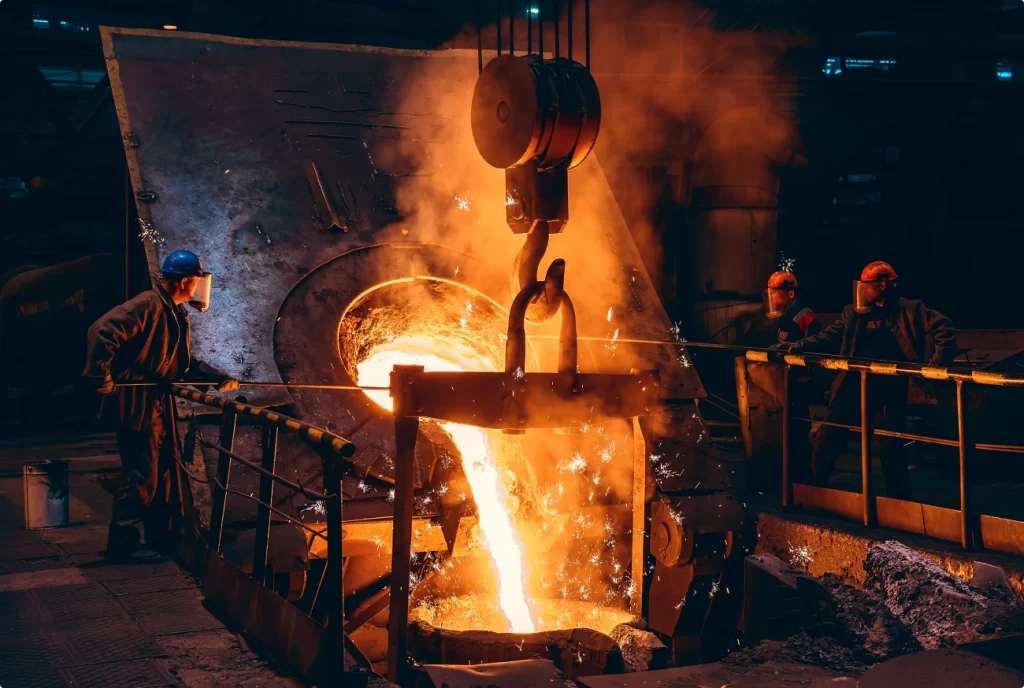
Leading Metal Casting Company in UAE
Based in Sharjah, UAE, CSG Extrusion is a trusted name in the metal casting industry. Our casting services are used in a wide range of sectors, including:
- Construction
- Automotive
- Electrical
- Packaging
- Marine
- Crusher Plants
Metal Casting We Offer
1. Sand Casting
Ideal for large, heavy parts.
Cost-effective and widely used.
2. Investment Casting
Best for intricate designs and tight tolerances.
Perfect for aerospace, medical, and precision components.
3. Die Casting
High-speed production.
Excellent surface finish and dimensional accuracy.
